A Comprehensive Overview to the Plastic Shot Molding Innovation
Plastic injection molding stands as a cornerstone of contemporary manufacturing, using unrivaled performance and precision in the manufacturing of complex plastic parts. As the landscape of manufacturing progresses, understanding the future trajectory of shot molding comes to be progressively imperative.
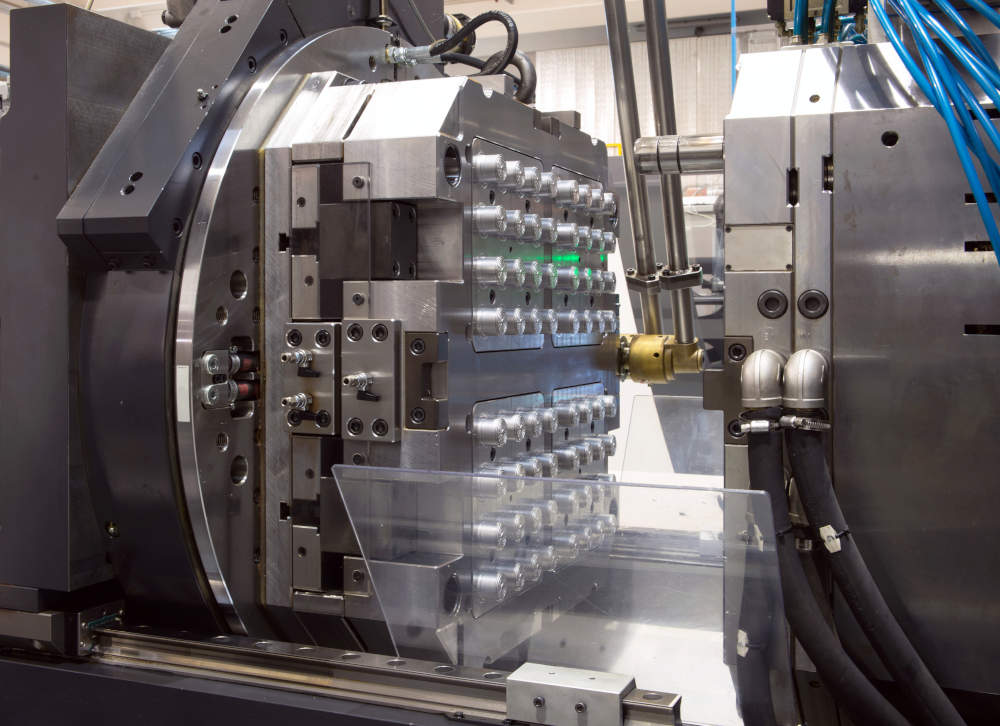
Review of Plastic Shot Molding
Plastic shot molding is an extensively utilized manufacturing process that enables the efficient production of complex plastic get rid of high precision. This innovation has become a foundation in different markets, including automobile, consumer goods, and electronics, owing to its ability to generate huge amounts of components swiftly and cost-effectively.
The process involves melting plastic granules and injecting the molten product right into a pre-designed mold and mildew. When cooled, the mold is gotten rid of to disclose the completed element, characterized by its intricate details and harmony. The adaptability of materials used in plastic shot molding, varying from thermoplastics to thermosetting polymers, enables producers to tailor items to meet certain needs, such as stamina, versatility, and resistance to warmth or chemicals.
Additionally, the efficiency of this approach minimizes waste and minimizes manufacturing expenses, making it an attractive choice for companies intending to enhance their manufacturing procedures. As technology breakthroughs, developments such as multi-material shot molding and the combination of automation remain to improve the capacities of plastic injection molding, making it possible for the development of increasingly advanced items that meet the needs of modern markets.
The Shot Molding Refine
Injection molding is an advanced manufacturing method that entails several important steps to transform raw plastic products right into completed items. The procedure begins with the preparation of plastic pellets, which are fed right into a warmed barrel. Here, the pellets are thawed and co-opted to achieve an uniform thickness.
As soon as properly heated up, the liquified plastic is injected into an exactly crafted mold and mildew under high pressure. This step is important, as it permits the product to fill up every dental caries of the mold and mildew, ensuring the final product properly mirrors the desired design. The injection time should be very carefully regulated to stop problems and make sure reliable product usage.
After the mold and mildew is loaded, it undertakes a cooling stage, where the plastic strengthens right into its last form. This cooling procedure can differ in period relying on the density and intricacy of the component. As soon as cooled down, the mold and mildew opens up, and the ended up item is expelled.
Secret Advantages of This Innovation
One of the most considerable advantages of injection molding technology depends on its capacity to produce high volumes of consistent and precise components with marginal waste. This performance originates from the computerized nature of the procedure, which dramatically lowers manual work and the capacity for human error. Consequently, manufacturers can achieve a high level of repeatability in their result, making sure that each part meets stringent top quality requirements.
One more key advantage is the adaptability of materials that can be used in shot molding. A vast variety of thermoplastics and thermosetting polymers can be molded, enabling customized buildings to fit specific applications. The innovation supports elaborate layouts and complex geometries, which can be testing to achieve with various other manufacturing approaches.
The preliminary financial investment in mold and mildews might be high, but the long-term savings in material waste and labor make injection molding an economically feasible alternative. These benefits strengthen injection molding's position as a preferred manufacturing process across various industries - Plastic Injection Molding.
Applications Across Industries
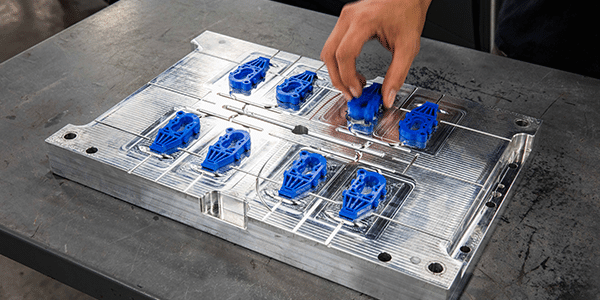
In the clinical field, shot molding is crucial for making premium, clean and sterile elements, consisting of syringes, surgical tools, and housings for medical tools. The ability to keep tight tolerances and generate complex geometries makes it an excellent choice for these applications. The packaging market advantages from shot molding by producing a large array of containers, closures, and dispensers that are both efficient and economical.
The toy market depends greatly on shot molding to create colorful, resilient, and risk-free items that interest children. Lastly, the building market makes use of shot molding for generating numerous fixtures, fittings, and components that add to both functionality and style. Generally, the wide variety of applications shows the important function of injection molding innovation in advancing different industries.
Future Trends in Injection Molding
Embracing advancements in technology, the future of shot molding is positioned for substantial improvement driven by advancements in materials, automation, and sustainable practices. Among one of the find out here now most remarkable fads is the advancement of bio-based and recycled polymers, which not only reduce dependence on fossil gas but additionally lessen environmental influence. As makers significantly prioritize eco-friendly solutions, these products are ending up being much more prevalent in production.
Automation is an additional crucial trend forming the industry. The assimilation of robotics and synthetic knowledge into the shot molding click for more info process boosts accuracy, manufacturing, and effectiveness speed. Smart manufacturing facilities equipped with IoT gadgets allow for real-time tracking and anticipating maintenance, decreasing downtime and maximizing operational processes.
Furthermore, the change towards personalized and small-batch manufacturing is gaining momentum. Advanced modern technologies such as 3D printing Discover More and additive production enable fast prototyping and the production of complex geometries that were previously unattainable. This shift enables firms to respond much more successfully to market needs and customer preferences.
Conclusion
In final thought, plastic shot molding modern technology stands for a cornerstone of modern manufacturing, using effectiveness and convenience in generating complex parts across diverse industries. The comprehensive assessment of the shot molding procedure highlights its important stages and benefits, while the expedition of applications emphasizes its prevalent importance. Arising trends, including sustainability and automation, indicate a promising future for this technology. Proceeded innovations are most likely to boost manufacturing abilities and environmental considerations, shaping the landscape of production.
Plastic injection molding stands as a cornerstone of contemporary manufacturing, offering unrivaled performance and precision in the production of facility plastic elements (Plastic Injection Molding). The versatility of products used in plastic shot molding, ranging from thermoplastics to thermosetting polymers, permits makers to tailor items to meet details demands, such as toughness, versatility, and resistance to warmth or chemicals
Injection molding is an innovative manufacturing method that entails a number of essential steps to change raw plastic materials into ended up products.The adaptability and performance of injection molding innovation have actually led to its widespread adoption throughout numerous markets.In verdict, plastic injection molding innovation stands for a cornerstone of contemporary production, offering effectiveness and adaptability in generating complex parts throughout varied sectors.